Mechanical Plating
Mechanical Plating and Galvanizing
Mechanical Galvanizing is a term used to identify a mechanical plating process that produces plating thicknesses greater than 0.001 inches.
- Mechanical Plating 0.0002 to 0.0009 inches.
- Mechanical Galvanizing 0.001+ inches
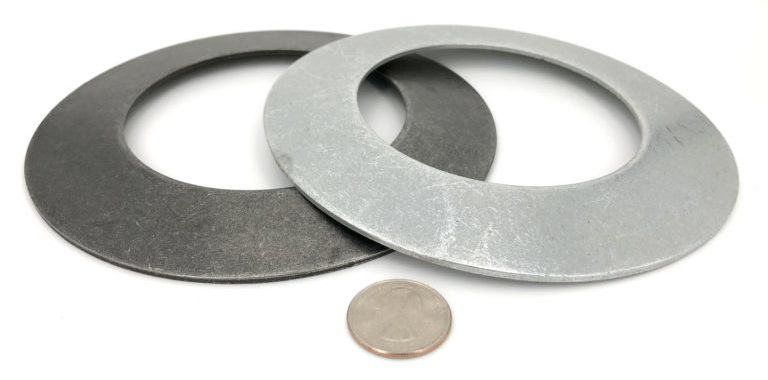
Coating Materials
We currently offer the following materials for mechcanical plating:

Zinc

Tin

Tin-Zinc

Tin-Zinc-Aluminum
Chromates and Passivates
We currently offer the following materials for mechcanical plating:
- Yellow (Hexavalent or Trivalent)
- Clear Trivalent
- Black (application dependent)
- Olive Drab
ASTM B695 Specifications
The following tables contain specifications from the ASTM B695 mechancla plating standard.
ASTM B695 Classification | Minimum Plating Thickness |
Class 5 | 5 µm ≈ .0002 in |
Class 8 | 8 µm ≈ .0003 in |
Class 12 | 12 µm ≈ .0005 in |
Class 25 | 25 µm ≈ .001 in |
Class 40 | 40 µm ≈ .0015 in |
Class 50 | 50 µm ≈ .002 in |
Class 55 | 53 µm ≈ .0021 in |
Class 65 | 66 µm ≈ .0026 in |
Class 70 | 69 µm ≈ .0027 in |
Class 80 | 81 µm ≈ .0032 in |
Class 110 | 107 µm ≈ .0042 in |
Source: ASTM B695
Class | Type I* | Type II** |
5 | 36 | 72 |
8 | 56 | 72 |
12 | 96 | 96 |
25 | 192 | 195 |
40 | 250 | 250 |
50 | 300 | 300 |
*Plain Zinc
**With Chromate Conversion Coating
Source: ASTM B695
Other Specifications
In addition to ASTM B695 specifications we can meet the following specifications:
- AASHTO – AASHTO M298-97
- ASTM – ASTM B695-00
- ISO – ISO 12683
- Chrysler Corporation – PS-1536
- Ford – ESF-M1P37-A
- General Motors – GM4344M & GM4345M
- John Deere – JDM F22
- United States of America – MIL-C-81562B
- RoHS Compliance
Please inquire about mechanical plating specifications that are not included in the list above.
Hydrogen Embrittlement
One of the primary benefits to mechanial plating is the elimination of hydrogen embrittlement.
Hydrogen embrittlement is a phenomenon in which a material experiences a significant reduction in ductility and tensile strength when atomic hydrogen diffuses into the material.
Hydrogen in its atomic form diffuses interstitially through the crystal lattice, and concentrations as low as several parts per million can lead to catastrophic brittle failure in normally ductile material. Martensitic steels are especially vulnerable to hydrogen embrittlement.
Electroplating is one of the few process that induce hydrogen embrittlement. This makes it necessary to add a post-plating baking process to drive out any dissolved hydrogen.
Mechanical plating eliminates the risk of hydrogen embrittlement and also eliminates the need for any post-plating risk reduction processes.
Resin Impregnation
Resin impregnation is a process of sealing of porosity which occurs in manufacturing processes such as casting and sintering. Through vacuum and pressure methods, polymer resin is forced into the porosity and then cured to form a pressure tight part.
Advantages of Resin Impregnation
- Eliminates porosity
- Eliminates bleedout
- Impregnation prior to electroplating, lacquering, and baked enamel finished eliminates bleedout from acid etches and electrolytes. Gassing and blistering by materials absorbed into the porosity is also eliminated
Materials we resin impregnate
- Powder Metal Parts
- Castings
Specifications
- MIL-STD-276
- MIL-I-17563
More Services
Dive deeper into our service ecosystem and find the perfect solution for you.
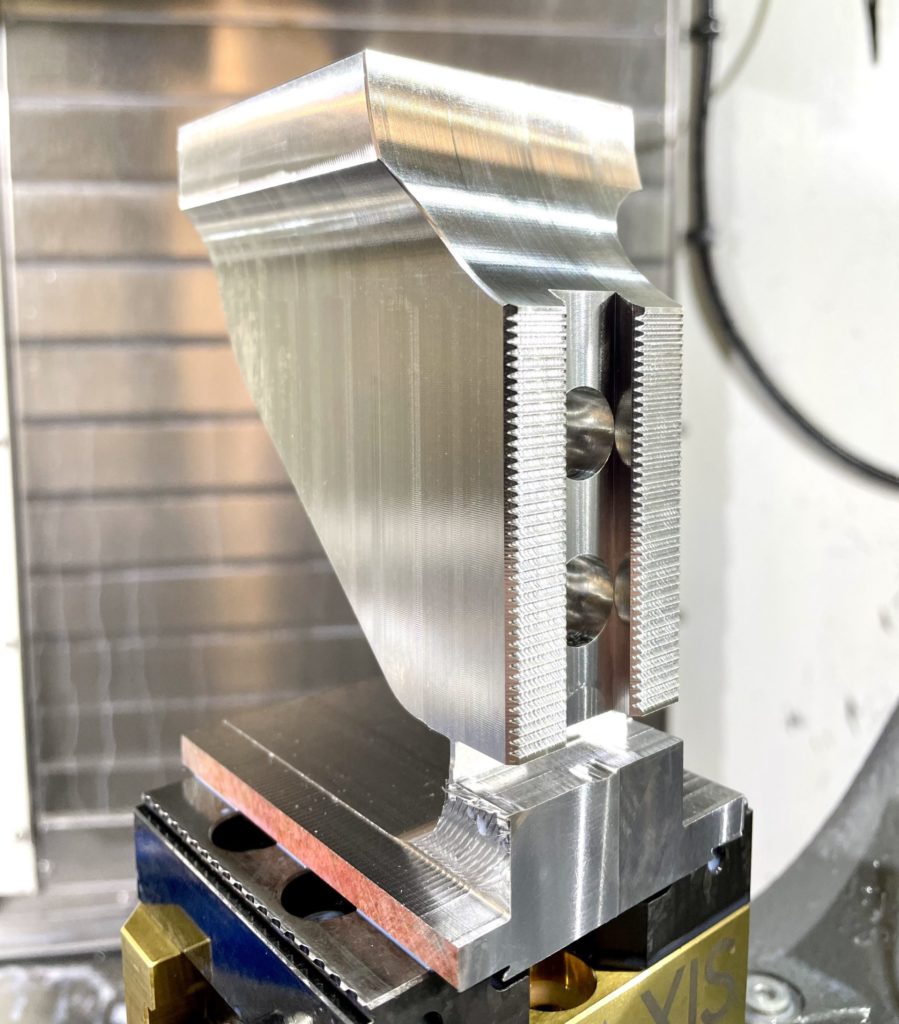
CNC Machining
Precise, repeatable, and efficient manufacturing of complex parts with high accuracy and speed.
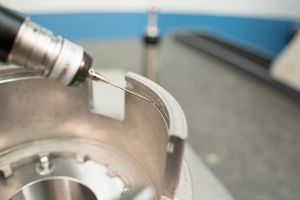
Quality Control
State-of-the-art quality control lab.